妥協したくない。そのために選んだ内製化。

96時間もの工程をかける、妥協なきアクリル成形
カットモデルで本体部品と同じくらい重要な役割を果たしているのが、カット部分に付けられているアクリル板。ただのフタではなく、元の部品の形をイメージさせつつ、中の部品を見せる必要があります。このアクリル板の造形において、日産のカットモデルは抜群に高い評価を得ています。
秘訣は、アクリル板の1枚板から削り出して作り上げていく、その製法。1つの部品を作るのに平均96時間もかけて製作する工程は、一見すると割に合わないようにも思えます。しかし、カットモデルチームを取りまとめる山崎はこう言います。
「透明なフタ部分にどんな素材を使い、どのような製法で作るのか。今のアクリル板にたどり着くまでに多くの素材や製法を試しました。しかし、仕上がりの美しさで今の製法に優るものはありません」(専門主任:山崎)
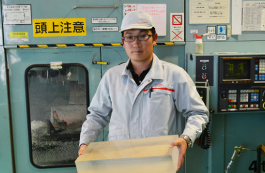
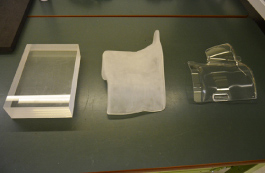
初の完成品が与えてくれた達成感と自信
別の製法との差がもっとも出るのは「いつまでも透明で見やすい」という点。同じアクリル板を使っていても、製法によっては表面が波打ったり、数ヶ月後に黄色く変色してしまったりします。数々のテストを経て、一切妥協することなく選んだ方法は、すべてを自分たちの手で作り上げること。その製作はCAD製作を担当している石田が、内製化開始当初から兼任しています。
「アクリル成形は社内でも初めて取り組む作業だったので、とにかく試行錯誤でした。でも、初めて完全内製化したジュークのトルクベクトルがカタログに掲載されたとき、ものすごい達成感と自分たちのやり方に対する自信がつきました」(石田)
彼らが業界随一と胸を張るアクリル板の仕上がり。その違いは、ぜひあなた自身の目で見て確かめてください。
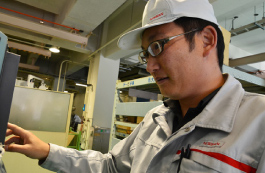
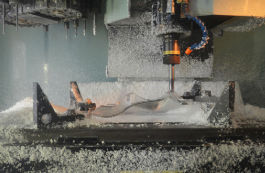